Cemento
Holcim (Svizzera) SA offre un ampio assortimento di cementi e materiali aggiuntivi, utilizzabili nelle applicazioni tecnico-costruttive più svariate. Oltre alla nostra ampia offerta di cementi standard e speciali, sviluppiamo anche cementi "su misura", adattati in modo ottimale alle esigenze specifiche del cliente, da un punto di vista tecnico ed economico. Grazie alla nostra infrastruttura flessibile di produzione e alla logistica distributiva affidabile, siamo in grado di fornire in qualsiasi momento cementi "su misura" anche in quantità ridotte.
HolcimNow: cemento e ordini semplici
Holcim continua a promuovere la digitalizzazione. Ad aprile, l’azienda ha lanciato la nuova piattaforma digitale HolcimNow, che consente ai clienti di ordinare il cemento online e attraverso un’app per smartphone. Possono inoltre monitorare in tempo reale lo status delle consegne e apportare adeguamenti a posteriori.
HolcimNow sfrutta i vantaggi della digitalizzazione: il software rileva infatti in tempo reale tutti i dati e le interazioni dai sistemi operativi di Holcim. I clienti possono quindi visualizzare in qualunque momento lo status delle proprie consegne senza alcun ritardo. HolcimNow offre costantemente la massima trasparenza e l’opportunità di gestire ed elaborare a posteriori il mandato. È possibile utilizzare la piattaforma HolcimNow sia da computer che attraverso l’app per dispositivi mobili. Non è necessario alcun account Google Play o Apple Store.
Con l’app HolcimNow:
- avrete una panoramica di tutti i vostri siti e dello status attuale dei rispettivi ordini
- potete generare nuovi ordini in modo semplice e rapido
- potete monitorare, adeguare e annullare gli ordini attuali
- potete scaricare documenti e rapporti in formato elettronico
- ricevete notifiche e bolle di consegna
- beneficiate del supporto del team Holcim
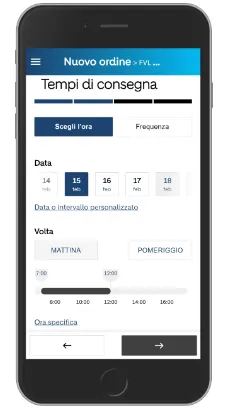
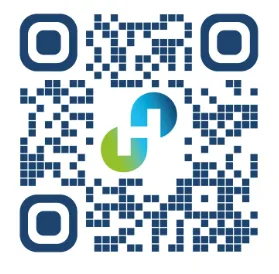
Ora iniziate
Effettuate il login sul vostro PC o scansionate il codice QR con il vostro smartphone. Selezionate «Registrati» per avviare il vostro account utente. Qualora abbiate bisogno di assistenza telefonica, rivolgetevi al vostro solito interlocutore per l’ordinazione del cemento al numero 0800 55 95 98.
Cos’è il cemento?
Il cemento è una polvere grigia a base di calcare cotto e argilla, dotata di proprietà idrauliche.
Non appena questa viene mescolata con l’acqua, si verifica una reazione chimica che provoca l’indurimento della miscela. Il cemento funge quindi da legante e viene lavorato con sabbia, ghiaia e additivi per formare il calcestruzzo, il materiale edile più importante della nostra epoca. Oggi il cemento si fabbrica in tutto il mondo con lo stesso procedimento.
Come si produce il cemento?
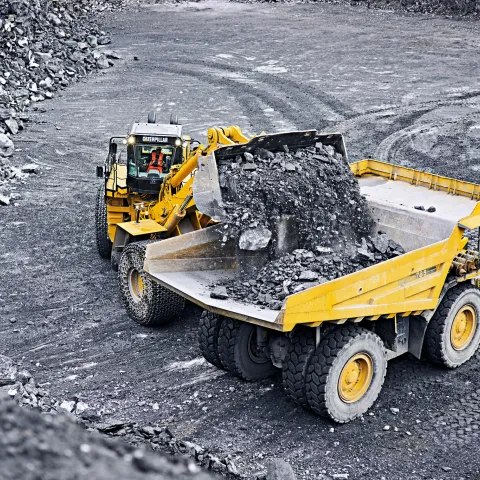
Cava
Il calcare (carbonato di calcio) e la marna vengono estratti nella cava dai minatori mediante brillamento. A tal fine essi scavano dei fori profondi nella roccia e li riempiono di esplosivo. Dopo una tempistica calcolata con precisione, le cariche vengono innescate. La tecnica di brillamento moderna limita le vibrazioni e porta a un crollo “ordinato” della parete.
Trasporto al frantoio
I detriti ottenuti dal brillamento vengono trasportati al frantoio mediante pale caricatrici gommate e camion ribaltabili. Potenti frantoi a ganasce o a martelli triturano i frammenti di roccia, la cui lunghezza può superare il metro, generando pietre della dimensione di una noce fino a un pugno. In alcuni casi il materiale, ad esempio argilla o marna, deve essere essiccato per garantire una corretta frantumazione, a causa dell’umidità risalente dal terreno.
Trasporto al cementificio
Il materiale grezzo frantumato viene poi trasportato dalla cava al cementificio. Di solito il trasferimento avviene attraverso nastri trasportatori, a volte mediante ferrovia, camion o altro mezzo di trasporto adeguato.
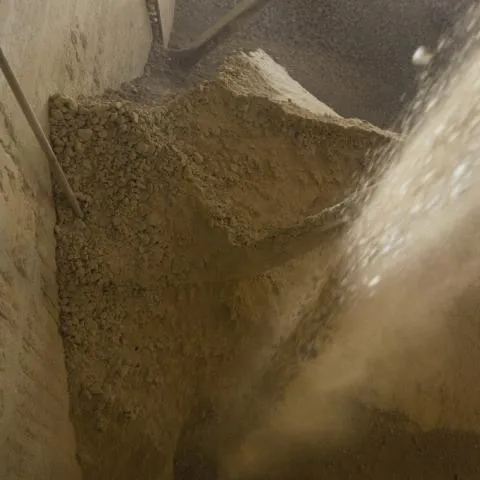
Letto di miscelazione
Il materiale grezzo per la produzione del cemento deve essere composto da una determinata miscela di calce, ossido di silicio, ossido di alluminio e ossido di ferro. I componenti frantumati, calcare e marna o argilla, vengono miscelati con cura (preomogeneizzati) distribuendo il materiale a strati nella corretta proporzione su un lungo mucchio, il letto di miscelazione. Questo letto di miscelazione viene poi nuovamente demolito prelevandone sezioni verticali. Il materiale così premiscelato è pronto per la triturazione.
Mulino del crudo
Il mulino del crudo macina il materiale crudo preomogeneizzato. Al suo interno, grandi rulli premono su un piatto rotante e schiacciano il materiale grezzo che vi si interpone, fino a ottenere la consistenza farinosa desiderata. Quando il materiale è sufficientemente fine, viene estratto attraverso il flusso di aria calda dei gas di scarico del forno, che essiccano il materiale all’interno del molino. La farina cruda passa attraverso i cosiddetti setacci, una sorta di filtri. Attraverso dei tubi, giunge poi all’apposito silo. Il processo di macinazione, separazione e insufflazione nel silo della farina cruda continua il processo di omogeneizzazione.
Dispositivo di filtraggio
L’energia termica impiegata viene sfruttata in modo efficiente: i gas di scarico del forno vengono impiegati per essiccare la farina cruda nel mulino del crudo. Il flusso di aria calda trasporta anche la farina sufficientemente fine fuori dal mulino. Nell’impianto di filtraggio, in cui si impiegano tubi flessibili in tessuto sottile o feltro agugliato, le particelle di polvere vengono trattenute prima che i gas di scarico si riversino all’esterno.
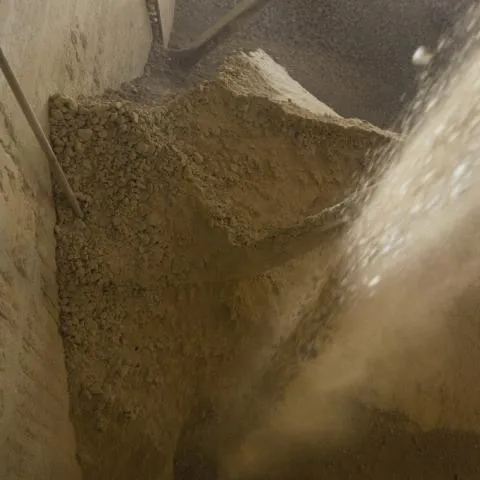
Preriscaldatore
I preriscaldatori a ciclone sono il sistema ottimale per riscaldare la farina cruda prima che giunga nel forno rotante. I gas di scarico del forno riscaldano la farina cruda in controcorrente in modo molto efficiente, tanto che questa risulta già calcinata all’ingresso nel forno fino al 20 - 40%, ovvero trasformata in calce viva. La calce viva si ottiene dissociando dal calcare l’anidride carbonica legata.
Forno rotante
Il forno rotante è creato in modo da garantire la massima efficienza nel passaggio del calore dal combustibile bruciato (la fiamma) alla farina cruda preriscaldata. Già nel preriscaldatore la farina raggiunge temperature prossime ai 1000°C. Nel forno rotante la temperatura della farina sale ulteriormente fino a circa 1450°C. A questi valori, i minerali in essa contenuta si trasformano e vetrificano mutandosi in clinker, prevalentemente cristalli di silicato di calcio.
Raffreddatore del clinker
Successivamente il clinker vetrificato dev’essere raffreddato molto rapidamente. A tal fine viene prelevata aria dall’atmosfera, che viene poi soffiata attraverso lo strato di clinker sparso sulla griglia del raffreddatore. Mentre l’aria fredda abbassa la temperatura del clinker, essa si riscalda e viene convogliata nel forno come aria di combustione preriscaldata. Questo ricupero del calore garantisce lo sfruttamento ottimale dell’energia impiegata. Il clinker, la cui temperatura è ancora oltre i 100 °C, viene portato fuori dal raffreddatore su un tappeto a maglie articolate.
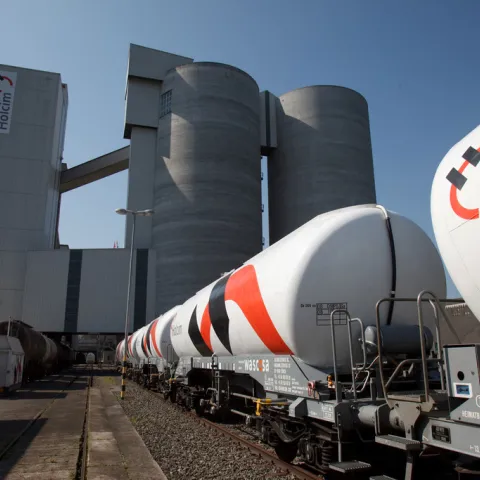
Silo del clinker
Il clinker raffreddato viene convogliato dai nastri trasportatori metallici in grandi sili o in un capannone, dove verrà conservato fino alla macinazione per la produzione del cemento.
Mulino del cemento
Le sfere di acciaio presenti nel mulino del cemento macinano il clinker con l’aggiunta di circa il 5% di gesso naturale o sintetico alla polvere di cemento vera e propria. Si possono miscelare insieme anche altri additivi simili al cemento come loppa granulata, cenere leggera o pozzolana, per modificare le caratteristiche del cemento per applicazioni speciali.
Logistica
Il cemento preparato viene imballato in sacchi e messo in commercio, oppure trasportato direttamente ai clienti mediante autosili. La modalità di spedizione varia a seconda delle peculiarità del sito e normalmente avviene via treno, camion o nave.